浮托安装是利用海上潮汐的自然力和船舶精确调载相结合的方式进行安装,类似于举重运动员“挺举”。以恩平20-4平台安装为例,该方式可将平台运输速度提高1倍,海上安装作业所需的气候窗口可由48小时缩短为24小时,作业效率大大提高。
海上油田建设离不开钻采平台,但钻采平台的安装并非易事,其单层甲板面积相当于多个篮球场,重达上万吨。安装这个庞然大物就像在波涛汹涌的海面上进行“倒车入库”。
日前,在广东珠江口盆地水深近百米的海域,天津港保税区企业海洋石油工程股份有限公司(以下简称海油工程)运用我国自主创新设计的动力定位浮托技术,成功完成恩平20-4钻采平台的建设,创造了国内海上油气平台动力定位浮托安装重量的新纪录,同时也填补了我国这项技术的空白,这对于保障国家安全、建设海洋强国具有重要意义。
动力定位浮托安装如在海上“倒车入库”
恩平20-4钻采平台是中国海油恩平15-1油田群产量最高的平台,由我国自主设计、建造及安装,可实现钻修井、智能采油、油气水综合处理以及伴生气回收利用等多项功能。
平台由上部组块和导管架两部分组成,其中导管架高度104米、重量近1.2万吨。
为了让导管架固定在百米深的海底,海油工程项目团队将12根长度近145米、直径2.4米的钢桩打入120米深的海床之下,确保这个合体后总重超过2.7万吨的钢铁巨人能够在超强台风下稳如泰山。
底座稳固了,但项目团队迎来了更大的挑战。
“通常来说,上部组块会采用海上浮吊的技术来进行安装。但恩平20-4的上部组块单层甲板实在太大了,面积相当于9个篮球场,重达15463吨。” 海油工程恩平油田群开发工程总包项目经理盛向明介绍说,“这个重量超过国内海上浮吊的能力极限,因此我们选定采用动力浮托技术进行海上安装。”
“浮托安装是利用海上潮汐的自然力和船舶精确调载相结合的方式进行安装,类似于举重运动员‘挺举’。”盛向明解释,以恩平20-4平台安装为例,该方式可将平台运输速度提高1倍,海上安装作业所需的气候窗口可由48小时缩短为24小时,作业效率大大提高。
方法有了,但是把如此庞然大物“挺举”上去难度不小。而且之前我国从未自主实施过动力浮托技术工程,从方案设计、计算分析到施工等都由外国公司负责。
“动力定位浮托安装过程相当于开着一辆长度超过220米、宽度40多米、装载10000辆小汽车的超级卡车,在波涛汹涌的海面上进行‘倒车入库’,两侧间隙仅为10厘米,组块插尖与导管对接精度要求达到毫米级。”盛向明说,这对设计计算精准性、动力定位系统可靠性、操作人员技术水平等均提出极大挑战。
自主创新技术确保安装万无一失
为了实现动力定位浮托安装,项目团队对该技术进行了攻关,突破了大型平台动力定位浮托精确设计分析、三维仿真模拟、精准定位操作等多项关键核心技术。
首先,精确数值分析是对浮托项目从装船开始就进行装船、运输、浮托过程的计算分析,根据计算结果进行安装设计。
“早期数值分析都是请国外公司来完成的,收费高昂,而且不会给我们提供原始数据。”海油工程浮托技术专家秦立成说,由于作业过程的非平稳、力学特征的非线性、多体系统强耦合等特点,多体耦合时域分析技术是精准数值分析中的难点。
为此,项目团队的计算工程师依托工程项目进行技术攻关,通过反复试算,结合试验,一点点推敲出关键数据。特别是项目刚刚开始的时候,计算工程师为了确定核心参数,经常通宵计算和进行数据比对。最终项目团队开发了动力定位静力评估和时域分析软件,并且在项目中成功应用。
有了设计方案,为了确保万无一失,还需要三维仿真模拟让施工人员提前按照施工方案来演练,提前发现问题和风险,在项目上规避这些问题。
最终团队开发了动力定位浮托模拟系统,解决了动力定位算法、水动力算法、多体耦合算法,为三维仿真模拟提供了技术支持。
有了“线上”模拟演练,还需“线下”实操检验。对此,项目团队组织了多次技术方案交底及作业风险分析,持续细化施工计划,开展浮托过程仿真模拟和水池实验,提前对锚系布设、进船、对齐、载荷转移等工序进行预演,并针对锚缆失效进行应急演练。
为了确保“倒车入库”能够准确进入规定的位置,还需“精准定位操作”。施工之前,项目团队大量开展虚拟模型培训,并在施工海域对关键操作进行现场预演,持续提高动力定位操作水平。
“船舶设置‘一用一备’两套独立的定位系统,为浮托提供稳定、精确的‘倒车防撞雷达’,且专门设计新型护舷系统和桩腿耦合缓冲装置,以防碰撞造成损坏,确保施工过程万无一失。”秦立成说。
无惧海上风浪精准完成平台对接
尽管已经做了万全的准备,但在大自然面前人类还是显得如此渺小。
恩平20-4平台进行浮托前夕,施工海域下起大雨,晚上风力达到六级,最大浪高4米,现场施工作业一度面临取消。
为了确保精准“入库”,主作业船距离槽口30米之后,需要由“自动挡”调整为“手动挡”。由经验丰富的动力定位操作师精准控制船舶进行“倒车”,每5米就要停船一次进行校准,到达10米以内时,每1米就要停船校准一次。
完成“倒车入库”还仅仅是施工作业的第一步,作业船进入导管架槽口后,上部组块的8个插尖要对齐导管架的8个对接装置,高度误差不超过5个指甲厚度,中心水平偏差不超过3个玉米粒总长,难度堪比宇宙飞船和空间站对接。“相比空间站在几乎不受外力影响情况下进行对接,海上浮托还要克服海上风、浪、涌等一系列不利因素。”本次动力定位浮托主作业船海洋石油278船船长刘雪峰说。
施工过程中,项目团队对风浪及船舶运动进行实时监测,抢抓时间窗口,精准操控,仅用7小时就高效完成施工作业,最大水平高度误差仅5毫米,精度控制达到国际先进水平,为后续项目投产节省宝贵时间。
海油工程安装分公司副总经理贺辰表示,在本次作业中,我国首次使用自有船舶、自有人员独立自主完成全流程关键作业,成功掌握大型平台动力定位浮托方案编制、设计计算、仿真模拟、动力定位系统操作、海上安装和监测等成套核心技术,填补了我国动力定位浮托自主设计安装技术空白。
目前,海油工程建成了以亚洲最大浮托驳船“海洋石油229”、5万吨级动力定位半潜工程船“海洋石油278”等为代表的系列关键装备,攻克浮托安装多体耦合控制算法、数值模拟软件开发、关键数据精准预报等多项技术难题,实现了浮托桩腿耦合缓冲器等核心部件的国产化,实现了高位浮托、低位浮托、动力定位浮托等全天候、全序列、全海域主流浮托施工关键技术的自主化,掌握的浮托技术种类、作业难度和技术复杂性等位居世界前列,并进行了浮托前沿技术的研究开发,具备了在全球恶劣海况海域进行浮托作业的能力。
来源:科技日报 记者 陈 曦
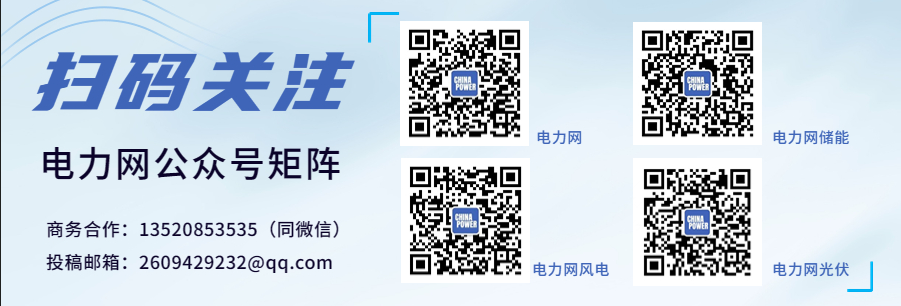
评论